Re-posted from MIT News. The exhibit was on view through June 20, 2013 in the Ray and Maria Stata Center, third floor, Room 32-338.
An expandable table. A collapsible CNC router. Motorized wheels whose diameter can enlarge and contract depending on the terrain. These are a few of the examples of “transformable design” now on display from the course, “Mechanical Invention Through Computation” led by visiting designer, engineer and inventor Chuck Hoberman. The seminar, co-taught with MIT professors Erik Demaine and Daniela Rus from the Computer Science and Artificial Intelligence Laboratory (CSAIL), was driven by a simple question: How can you create new transformable objects?
This is the question that has shaped Hoberman’s unique 20-year career at the nexus of art and science, design and engineering. In 1990, he patented the Hoberman sphere: a mechanism resembling a geodesic dome that was created from a series of scissor-like joints (similar to those found on a cherry picker) allowing the object to expand and contract. Since then, Hoberman has invented a variety of shape-shifting products ranging in scale from toys, shelters, stage sets, medical devices, sculptures, buildings and furniture. There seems to be no end to the potential applications for these kinds of dynamic products, which use kinematics — the geometry of motion — to produce surprising and unique movements.
With Demaine and Rus, the course investigated how this kind of mechanical invention could be further optimized using mathematical analysis and computational processes. According to the exhibit text, “The inventive process itself is ripe for innovation.” Like Hoberman, both Demaine and Rus have also built their careers researching reconfigurable forms, making breakthroughs in the areas of programmable matter and computational origami respectively. Together, they have developed a sheet that can assemble into three-dimensional shapes of its own accord — such as a boat or a paper airplane — similar to the way that proteins found in nature can fold and refold into complex shapes to achieve different behaviors.
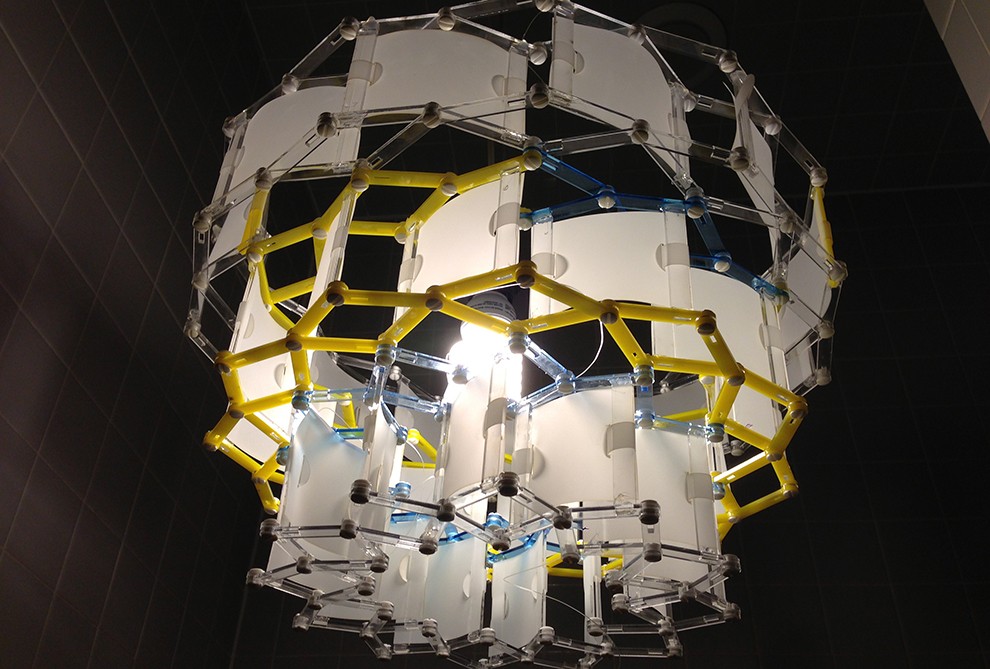
The resulting student projects ranged in scale and function, from pin joints that could only be seen with a microscope to large retractable tables. There was a DIY expandable lamp created completely from off-the-shelf materials; a foldable trapezoidal kite modeled after one designed by Alexander Graham Bell; a winged Phoenix-like sculpture based on a J.G. Ballard science fiction story; and a skirt that used “inflatable origami” to change size and shape. Every project was the result of continual prototyping with different types of designs and materials, employing methods both digital and physical.
This kind of mechanical intelligence is the wave of the future, as programming meets material to create supple and versatile new forms. In a world defined by flux, we increasingly require products and structures to be flexible, dynamic, and responsive to their changing environments. By transforming the process of invention — a creative act at the intersection of the technical, the scientific and the expressive — the course helped prepare the next generation of inventors for this challenge. “We’re really just beginning to scratch the surface,” Hoberman said at the exhibit’s opening.